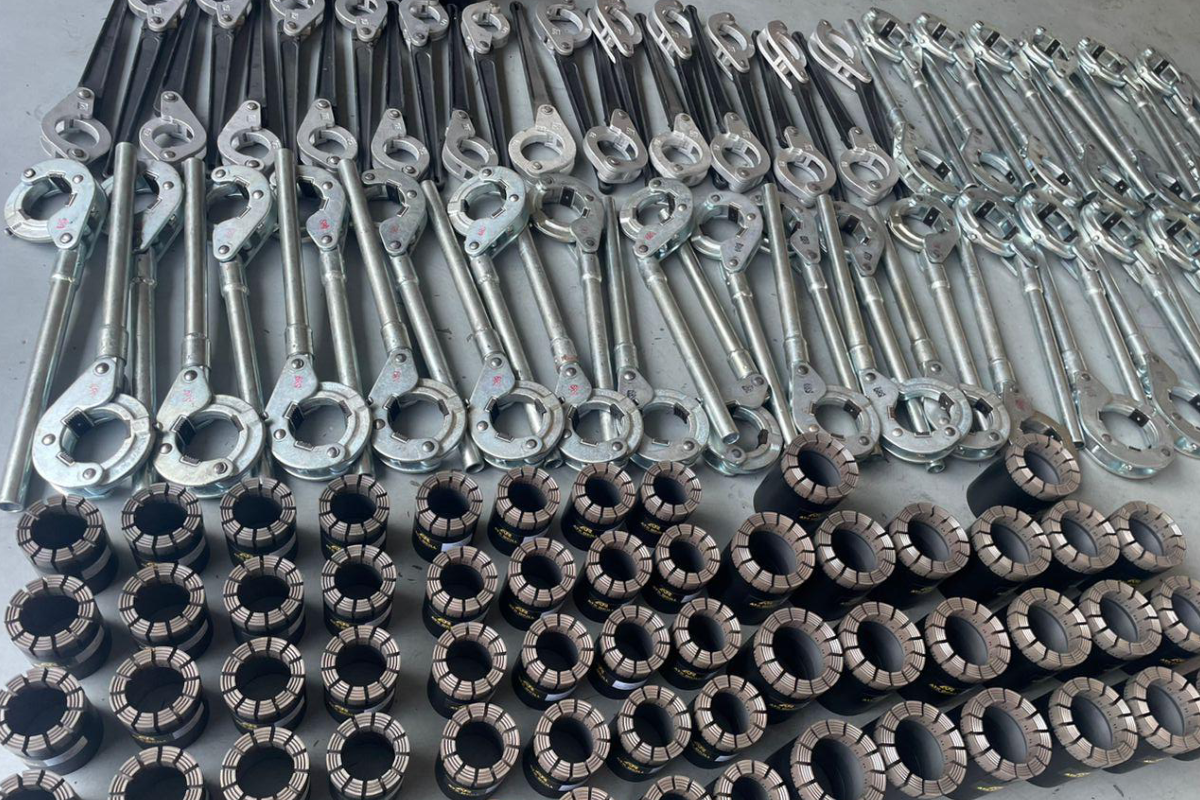
Drilling Rig for Your Geotechnical Projects
Choosing the right drilling rig is one of the most critical decisions you’ll make when undertaking geotechnical projects. Whether you’re conducting soil investigations, foundation design, or environmental studies, the right rig ensures accurate data collection, efficient operations, and cost-effectiveness. With so many options available, understanding the features, capabilities, and advantages of different drilling rigs can help you make an informed decision. In this blog, we’ll provide key insights and tips to help you select the best drilling rig for your geotechnical needs.
Understanding the Role of Drilling Rigs in Geotechnical Projects
Geotechnical drilling rigs are essential for subsurface investigations, allowing professionals to assess soil and rock properties, groundwater levels, and other geotechnical conditions. This data is crucial for construction, mining, and environmental projects, where understanding subsurface conditions informs project design and risk mitigation.
Depending on the depth, terrain, and type of investigation, different drilling rigs offer unique capabilities. Selecting the right rig can greatly impact the efficiency, safety, and accuracy of your geotechnical investigation.
Factors to Consider When Choosing a Drilling Rig
- Project Requirements
The first step in choosing the right rig is understanding your project’s specific requirements. Consider the following:
- Depth: How deep do you need to drill? Shallow site investigations may require lighter rigs, while deeper projects may need heavier-duty rigs.
- Soil and Rock Types: The rig’s capability to handle different soil and rock formations is crucial. If you’re dealing with soft soil, a lighter rig might suffice. For harder rock, a more robust rig designed for heavy drilling is necessary.
- Sample Size and Type: Some projects require soil samples for laboratory analysis, while others focus on in-situ testing. Choose a rig that supports the specific tools and testing methods your project requires.
- Drilling Method Compatibility
Geotechnical drilling involves different methods, each suited for specific conditions and project goals. Choose a rig that is compatible with your preferred drilling method:
- Auger Drilling: Best for shallow depths and soft to medium soil conditions. Auger rigs are relatively lightweight and easy to use.
- Rotary Drilling: Ideal for deeper drilling and harder rock formations. Rotary drilling rigs are versatile and can handle various soil types, making them suitable for more complex projects.
- Percussion Drilling: Used in hard rock formations, this method relies on hammering or chiseling through tough rock. Percussion rigs are necessary for projects requiring deep penetration into rock.
- Sonic Drilling: A newer technology that uses high-frequency vibrations to drill. Sonic rigs are efficient for certain soil types and can provide faster, cleaner samples.
- Rig Mobility and Access
The location of your project site is another critical factor. Geotechnical drilling rigs vary in size, mobility, and portability. In some cases, the terrain may be challenging, and you’ll need a rig that can be easily transported or maneuvered into difficult-to-reach locations.
- Truck-Mounted Rigs: These are ideal for projects with easy road access. They are larger and can handle heavier-duty drilling.
- Track-Mounted Rigs: These rigs offer enhanced mobility, making them ideal for rough or uneven terrain. They can be used in areas where traditional truck-mounted rigs may not reach.
- Portable Rigs: When working in remote or confined areas, smaller portable rigs can be disassembled and carried manually or with minimal equipment.
- Power and Efficiency
The power of the rig directly impacts its drilling speed and efficiency. Hydraulic-powered rigs offer better control and efficiency, especially for deeper or more complex drilling tasks. Consider the power output required for your specific project needs. Higher-powered rigs can handle tougher jobs more quickly, reducing operational time and costs. - Automation and Technology
Modern geotechnical drilling rigs come equipped with advanced features such as automated rod handling, GPS, data logging, and monitoring systems. These features improve safety, reduce labor requirements, and enhance the accuracy of the data collected. Automation is especially useful in large-scale projects where precision and efficiency are paramount.
Different Types of Drilling Rigs for Geotechnical Projects
- Auger Drilling Rigs
Auger rigs are commonly used for shallow drilling projects. They are highly effective in soft soils and can quickly retrieve samples for analysis. Auger rigs are lightweight, easy to operate, and cost-effective for small to medium-scale geotechnical projects, such as foundation investigations or environmental testing. - Rotary Drilling Rigs
Rotary rigs are versatile and can be used for drilling through both soil and rock. They are particularly useful in deep drilling applications where more robust equipment is required. Rotary drilling rigs are ideal for construction site investigations, groundwater studies, and mineral exploration. - Percussion Drilling Rigs
Percussion drilling rigs are designed to break through tough rock formations. They work by using a hammering action to chip away rock and are often used in hard rock environments. This method is slower but essential when drilling through challenging geological conditions. - Sonic Drilling Rigs
Sonic drilling rigs use high-frequency vibrations to penetrate the ground. This method is highly efficient, particularly in softer soils, and provides clean, continuous core samples. Sonic rigs are often used for environmental sampling, mineral exploration, and projects where precise core samples are needed. - Reverse Circulation (RC) Drilling Rigs
RC drilling rigs are popular in mining and exploration projects. They use dual-tube technology, allowing compressed air to push cuttings up the inner tube, ensuring uncontaminated sample retrieval. RC rigs are suitable for both shallow and deep drilling applications where accurate, uncontaminated samples are critical.
Why Rig Durability and Maintenance Matter
A key factor in choosing the right drilling rig is its durability and ease of maintenance. A rig that requires frequent repairs or downtime can significantly impact project timelines and increase costs. Look for geotechnical drilling rigs built from high-quality materials with a proven track record of reliability. Additionally, ensure that spare parts and maintenance services are readily available to minimize downtime during your operations.
The Benefits of Choosing the Right Drilling Rig
- Increased Accuracy
The right rig for your project will allow for more precise drilling and better-quality sample retrieval, leading to more accurate subsurface data. Whether it's soil, rock, or water testing, the precision of the equipment directly affects the reliability of the results. - Operational Efficiency
Choosing a rig that aligns with your project requirements means less downtime and faster project completion. More efficient rigs reduce labor costs, fuel consumption, and operational time, which is critical for staying within project budgets. - Adaptability to Various Conditions
The versatility of modern drilling rigs ensures that you can adapt to changing site conditions. Whether you're working in soft soil, hard rock, or mixed formations, the right rig will allow you to seamlessly switch between different drilling methods as needed.
Why Choose ATR Drill for Your Geotechnical Drilling Rigs
At ATR Drill, we offer a wide range of geotechnical drilling rigs designed to meet the specific needs of your project. Our rigs are built for durability, precision, and efficiency, ensuring you can tackle complex geotechnical investigations with ease. Whether you need a rig for shallow soil sampling or deep rock drilling, we have the expertise and equipment to help you succeed.
For more information on our geotechnical drilling rigs, visit our Geotechnical and Soil Investigation Product Range or explore our Geotechnical Drilling Rigs.
Frequently Asked Questions (FAQs):
1. What factors should I consider when choosing a geotechnical drilling rig?
Consider factors such as project depth, soil and rock types, drilling method compatibility, rig mobility, and power when selecting a drilling rig.
2. What types of drilling rigs are best for geotechnical projects?
Popular types include auger, rotary, percussion, sonic, and RC drilling rigs, each suited for specific conditions and project goals.
3. How does rig power affect drilling efficiency?
Higher-powered rigs offer faster drilling speeds and can handle more complex drilling tasks, reducing operational time and increasing overall efficiency.
4. Why is rig mobility important in geotechnical projects?
Rig mobility ensures that your drilling equipment can easily access difficult or remote project sites, saving time and labor costs.
5. Where can I buy high-quality geotechnical drilling rigs?
You can purchase high-quality geotechnical drilling rigs from ATR Drill.
Visit our Contact Page for more details.